联系我们
- 全国免费服务电话
- 地址:永嘉县瓯北镇东瓯街道张堡工业区
- 电话:0577-67317379、67365232
- 手机:13868647363
- 邮箱:zhongtefamen@163.com
- 传真:0577-67317193
球墨铸铁阀门无冒口铸造的工艺方案
一、思路
在国内所检文献范围内,有关大口径球墨铸铁阀门无冒口铸造工艺技术方面,仅有厚大球墨铸铁飞轮铸造成形方法、球墨铸铁小口径(DN500以下)阀门无冒口铸造工艺技术、以及铸件造型用振动台、铸件用阻流涂料的研究及应用等文献报道。相关专利有:厚大飞轮铸造成形方法、铸件造型用振动台、铸件用阻流涂料的研究及应用、-60℃低温冲击球墨铸铁的制备方法等。本课题以大口径(DN2000)球墨铸铁阀门无冒口铸造为研究对象,研究大口径(DN02000)球墨铸铁阀门无冒口铸造的可行性。球墨铸铁材质为QT600-3,重约5250kg,结构较为对称,平均壁厚为30~50mm,最薄处壁厚为30mm,最厚处达到80mm。口径(DN2000)球墨铸铁阀门工作环境恶劣,要承受一定的压力,且铸件内部薄壁与厚壁交错相连,因此要求铸件内部不能有缩松、缩孔缺陷,采用传统的设计浇冒口系统很难对铸件内部厚壁部分进行补缩,最后在铸件内部易形成缩、松缩孔缺陷。 本课题首先对顺序和均衡凝固技术和无冒口工艺以及球墨铸铁的凝固特性进行分析,顺序和均衡凝固技术与无冒口铸造工艺的原理都是要求充分利用铸件内部的石墨化膨胀进行自补缩,浇注系统只是用于补缩铸件前期的液态收缩,浇注系统则需要在铸件内部发生石墨化膨胀时及时凝固关闭,防止由于石墨化膨胀将型腔内的金属液反补进入浇注系统;其次以口径(DN2000上)球墨铸铁阀门为对象,应用顺序和均衡凝固技术和无冒口铸造工艺对大口径(DN2000上)球墨铸铁阀门进行工艺设计:最后运用铸造模拟软件Procast对铸造工艺进行数值模拟,结果表明,采用顺序和均衡凝固技术和无冒口工艺设计,能消除原工艺存在的缩松、缩孔缺陷。另外,制订合理熔炼工艺,采用变频振动高强度砂型,得到合格致密的铸件。如下图DN1200的球墨铸铁镶铜圆闸门。
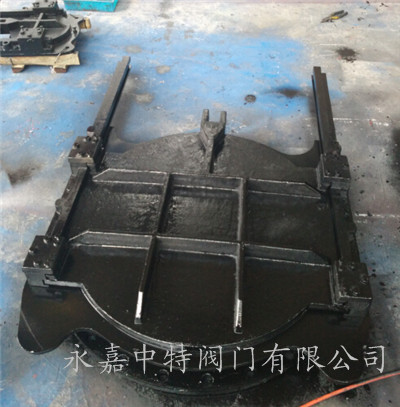
二、研究方案
1.工艺方面
模数M= V/A散热 = 728155/ 155159=4.69 cm≥2.5cm,另外加上化学成分的控制,孕育处理,铸型的刚度,浇注系统的设计,以及冷铁的使用等,通过优化工艺可以不需要冒口。采用半开半封闭式浇注系统,ΣF内∶ΣF横∶ΣF直=1.0∶2.5∶2.0,采用阶梯式浇注系统,浇注时先快浇后慢浇,形成梯度温度场,满足“顺序凝固”原则,易获得理想致密结晶铸件,铁液分散进入型腔,铁液从远离浇注系统的一端开始由远及近,由下往上顺序凝固,再加上辅助冷铁的作用达到同时凝固,整体上体现了均衡凝固理论。
(1)浇注系统设计 采用半封闭式浇注系统,直浇道底部采用过滤网,内浇道设置改为“阶梯式”,内浇道在贴着阀门中口砂芯外表范围均匀布置与铸件连接,且浇注系统不设置冒口,如图2所示。经过计算,设置12个内浇道,单个内浇道截面积为1.31cm2(a=23mm,b=21mm,c=10mm),查表取内浇道长度L内=150mm。设置2个横浇道分上下两层,单个横浇道截面为55cm2(a=55mm,b=44mm,c=53mm ),横浇道长2436mm。直浇道截面积为50cm2,直径为80mm。
浇注系统设计
实践证明,阶梯式要比中间浇注式方案优,根据流体力学理论,阶梯式铁液流入型腔平稳,型内不会出现飞溅现象,杂质和反应气体及二次造渣均能浮在铁液上表面;而中间浇注时铁液流入型腔会产生紊流、飞溅,气体、杂质及二次渣伴随铁液紊乱充型,不易上漂到表面,容易出现质量问题(如夹渣、气孔等)。另外,采用过滤网孔径的技术,浇注出的铸件产品晶粒细小,没有出现等轴晶、球状和粒状晶体的结构。
由于内浇道分布在阀门中口上下圆周部分,而且是阶梯式, 下法兰外表面放置冷铁,便于控制温度场分布,形成梯度温度场,保证上层内浇道以下部位自下至上满足“顺序凝固”原则,同时上法兰也放置冷铁,当金属液充满型腔时,内浇道迅速关闭,使上层内浇道以上部分实现同时凝固,达到均衡凝固,同时充分发挥石墨膨胀作用,可获得理想致密的铸件。
冷铁可选用生铁冷铁或石墨冷铁,H冷≥0.8δ件,冷铁间距应控制在25~35mm较为合适。
(2)浇注温度的选择 因无论规格大小,法兰(轴台)处壁厚尺寸均较大,所以浇注温度过低时易产生冷隔,浇注温度过高不易于温度场合理分布,铸件局部高温区易出现结晶粗大和缩孔、缩松缺陷。因此浇注温度不宜过高,且温度低可以减少液态收缩,因此浇注温度应控制在1310~1340℃较为合适。
2.化学成分控制
(1)化学成分 由于球状石墨对基体的削弱作用很小,故球墨铸铁中石墨数量的多少,对力学性能的影响并不显著,当wC在3.2%~3.9%变化时对力学性能无明显的影响,故在确定C、Si含量时,主要考虑保证其铸造性能,将CE选择在共晶成分左右,此时铁液的流动性能最好,形成集中缩孔的倾向大,铸件组织致密度高。由于铸件壁厚较均匀,但法兰较厚,CE过高时会产生石墨漂浮的倾向,为保证无冒口铸造工艺,充分发挥石墨化膨胀的自补缩作用,故CE的选择在共晶点附近,即4.6%~4.7%(由于球化元素的存在,球墨铸铁的共晶点已移至4.6%~4.8%附近)。Si含量的高低,直接影响球墨铸铁基体中铁素体的含量。Si能促进石墨化,增加铁素体含量,细化石墨,强化基体组织,但Si提高脆性转变温度,降低冲击韧度。因此,在选定高碳当量的前提下应采用高C、低Si的原则,最终确定将wSi控制在2.6%~2.8%较合适。
铁液中P含量偏高,会使凝固范围扩大,同时低熔点磷共晶在最后凝固时得不到补给,并使铸件外壳变弱,因此有增大缩孔、缩松产生的倾向,故P含量应控制在较低值。
RE残留量过高会恶化石墨形状,降低球化率,因此RE含量不宜太高。而Mg又是一个强烈稳定碳化物的元素,阻碍石墨化。由此可见,残留Mg、RE量过高会增加球墨铸铁的白口倾向,使石墨膨胀减小,另外当残留Mg、RE含量较高时,也会增加缩孔、缩松倾向,故残留Mg、RE含量也不宜过高。
化学成分含量如下:wC=3.45%~3.65%、wSi=2.2%~2.5%、wMn=0.25%~0.45%、wP≤0.08%、wS≤0.025%、wRE残=0.02%~0.04%、wMg残=0.035%~0.045%。
(2)球化剂和孕育剂选择 选择合适的球化剂和孕育剂球化剂。本项目选择重稀士和珠光体球化剂联合使用,孕育剂选择硅钡孕育剂效果较好。
(3)合金元素应用 为充分满足和提高物理性能,必要时可通过适当添在一些合金元素(如Cu、Sn、Ni等)。
3.现场操作工艺控制
(1)造型时控制铸型紧实度,造型中可变频率振动台震实,保证铸型刚度,保证在析出凝固过程中析出石墨膨胀而不产生型壁迁移,从而发挥自补缩作用,并且设置若干出液(气)桩,设置一根作为出液溢流桩。
(2)合箱前,型芯应反复缓慢烘烤,烘干烘透。
(3)浇注温度严格按工艺规定执行,球化处理后浇注温度应在1360~1380℃较为适宜,扒渣运送至铸型浇注时温度为1310~1340℃。
(4)浇注中待有铁液从出液桩出液时即停止作业。
结语
大口径(DN2000)球墨铸铁阀门无冒口铸造工艺设计与研发主要从以下几个方面考虑:
(1)采用高刚度的铸型,能够在铁液完全进入型腔后,型腔尺寸保持不变或者变化量极小。
(2)在不发生石墨漂浮的前提下,采用尽可能高的碳当量,适当的孕育,确保充分石墨化,最大限度地增大石墨化膨胀的体积增加量。
(3)采用阶梯式多道内浇道,使铁液分散进入型腔,内浇道以下部位实现顺序凝固,内浇道以上部位,并配合冷铁调节,尽可能使铸件各部位同时开始并同步进行冷却和凝固。
(4)大量使用冷铁,强化铸件冷却,使铁液进入型腔后,铸件外层迅速冷却、凝固,在内浇道及铸件心部的液态通道凝固封闭之前提早完成一部分收缩,形成体积空缺,及时从液态通道获取补缩液体,增大内浇道的流量(也即增大外部补缩量),提高浇注系统的补缩效果。
(5)适当降低浇注温度,减少液态体积收缩。
采用无冒口工艺,实现了极高的工艺出品率和较高的产品合格率。产品优良品率已达到98%以上,各项性能指标均能符合客户订货技术条件要求。
作者:柴知章、于鹏,安徽信息工程学院。
来源:《金属加工(热加工)》
如有更多阀门相关需要,请访问我们网站 www.zhongtefamen.com。